The Scientific Research Behind Porosity: A Comprehensive Overview for Welders and Fabricators
Recognizing the intricate mechanisms behind porosity in welding is vital for welders and makers aiming for impeccable workmanship. From the make-up of the base materials to the complexities of the welding process itself, a wide range of variables conspire to either worsen or relieve the presence of porosity.
Comprehending Porosity in Welding
FIRST SENTENCE:
Exam of porosity in welding reveals critical understandings right into the integrity and high quality of the weld joint. Porosity, defined by the presence of tooth cavities or voids within the weld metal, is a common problem in welding processes. These voids, otherwise appropriately attended to, can jeopardize the structural honesty and mechanical buildings of the weld, resulting in potential failures in the ended up product.

To detect and measure porosity, non-destructive testing methods such as ultrasonic screening or X-ray assessment are typically used. These strategies permit the recognition of inner flaws without jeopardizing the integrity of the weld. By analyzing the dimension, form, and distribution of porosity within a weld, welders can make informed choices to boost their welding processes and achieve sounder weld joints.

Variables Influencing Porosity Formation
The event of porosity in welding is influenced by a myriad of variables, ranging from gas securing effectiveness to the ins and outs of welding parameter settings. Welding specifications, consisting of voltage, existing, take a trip speed, and electrode kind, also impact porosity formation. The welding method utilized, such as gas metal arc welding (GMAW) or protected steel arc welding (SMAW), can affect porosity formation due to variations in warm distribution and gas protection - What is Porosity.
Impacts of Porosity on Weld High Quality
The check that presence of porosity additionally damages the weld's resistance to corrosion, as the entraped air or gases within the spaces can react with the try this site surrounding setting, leading to deterioration over time. In addition, porosity can prevent the weld's capability to hold up against pressure or effect, further endangering the general quality and integrity of the bonded framework. In critical applications such as aerospace, automotive, or architectural building and constructions, where safety and longevity are critical, the destructive effects of porosity on weld high quality can have extreme repercussions, find out this here highlighting the importance of lessening porosity through appropriate welding strategies and treatments.
Strategies to Reduce Porosity
Furthermore, making use of the suitable welding specifications, such as the appropriate voltage, present, and take a trip speed, is vital in stopping porosity. Maintaining a regular arc size and angle during welding likewise helps lower the probability of porosity.

Using the ideal welding strategy, such as back-stepping or utilizing a weaving motion, can likewise aid distribute heat uniformly and reduce the opportunities of porosity formation. By applying these methods, welders can successfully decrease porosity and create top quality bonded joints.
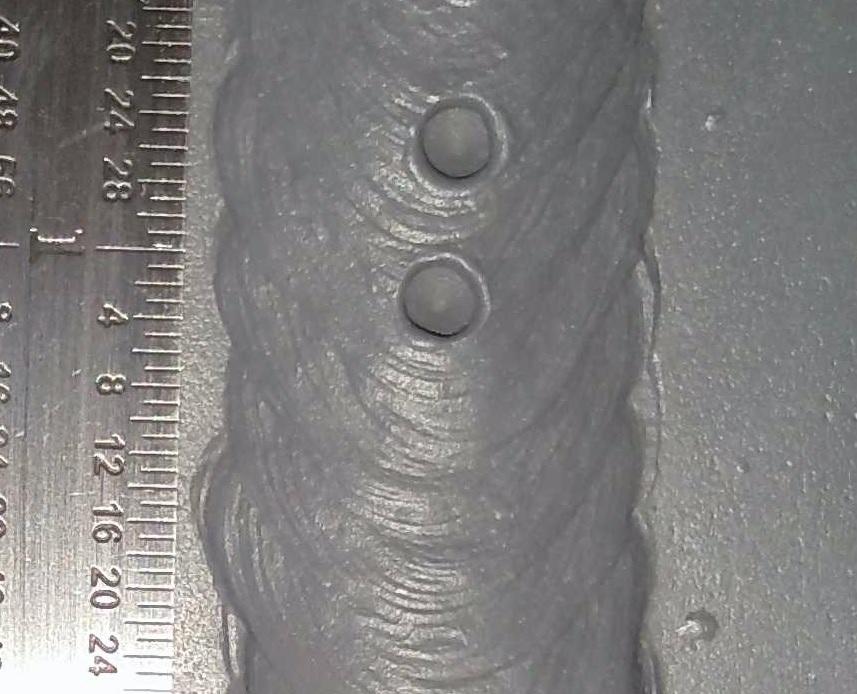
Advanced Solutions for Porosity Control
Executing sophisticated technologies and innovative approaches plays a crucial function in accomplishing premium control over porosity in welding procedures. Additionally, employing advanced welding strategies such as pulsed MIG welding or customized ambience welding can likewise help mitigate porosity concerns.
One more innovative remedy involves making use of innovative welding tools. Using devices with integrated attributes like waveform control and innovative power resources can boost weld high quality and decrease porosity dangers. Furthermore, the application of automated welding systems with accurate control over specifications can substantially lessen porosity issues.
Moreover, including innovative monitoring and inspection technologies such as real-time X-ray imaging or automated ultrasonic testing can assist in spotting porosity early in the welding procedure, enabling instant restorative activities. Generally, incorporating these innovative remedies can significantly boost porosity control and boost the general high quality of welded parts.
Final Thought
In final thought, understanding the scientific research behind porosity in welding is vital for welders and fabricators to create top notch welds - What is Porosity. Advanced services for porosity control can even more enhance the welding procedure and make certain a solid and trusted weld.
Comments on “What is Porosity in Welding: Key Elements and Their Influence On Weld Top Quality”